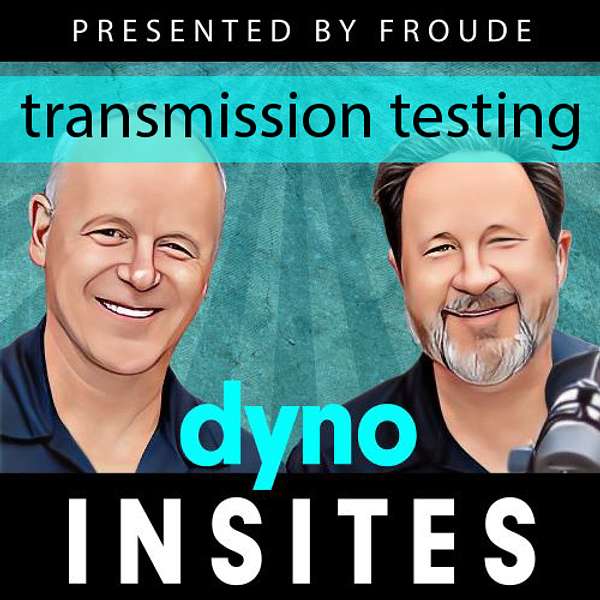
dyno INSITES
Whether you are an engineer responsible for designing an engine test cell, an operator, an engineering student, or simply a person interested in engine testing, the Dyno Insites podcast is your source for real-world, practical engine dynamometer conversation. We don't engage in lengthy banter. We get right to the point with a focus on educating our audience.
Gathering information about dynamometer test systems can involve scouring through numerous technical websites and often the information lacks the practical application aspect one seeks to fully understand engine test systems.
Join hosts and Froude engineers, Mike Golda and Chris Middlemass as they share a combined 60 years of engine test cell experience during this informative, 10 - 30 minute, monthly podcast. By the way, we don't have a fancy sound studio, we're recording in the back electronics lab in our Novi, MI location. We do our best to edit out obvious distracting noises, but we are all here and working, so the podcast may catch a bit of background noise-- perhaps a door closing or other sounds of a busy facility!
If there's a topic you'd like us to cover, or if you would like to be a guest on dyno insites, please email podcast@froudedyno.com.
Information on Froude dynamometers can be found at https://froudedyno.com.
Dyno Insites. Powering Your Engine Dynamometer Knowledge.
dyno INSITES
Shifting Gears: AC Dynos & Transmission Testing
In this episode, we highlight the versatility of AC dynamometers. Mike Golda interviews Bill Collet, a subject matter expert in the use of AC dynos in transmission testing. Bill explains why we test transmissions, how we test them, and what the future holds for transmission testing.
Thank you for listening! If there's an engine testing topic you'd like us to cover in future episodes, or you'd like to be a guest on dyno INSITES, please email podcast@froudedyno.com.
Visit Froude's website for more information on dynamometer test systems.
Diane Nossal:
Thank you for tuning in to Dyno Insites. In today's episode, we have a guest. Bill Collet joins Mike Golda today to talk about AC dynos and transmission testing.
Mike Golda:
So I'm excited today because we have a special guest with us. His name is Bill Collet. I've known him for a few years in our prior employment. He currently works at Froude with us, and I'd like him to talk a little bit about his background before we dive into today's podcast.
Bill Collet:
Hello, Mike. Well, I've been in the business for 30 plus years. All of my career has all been in testing. So I started the first ten years where I was doing wind tunnel aerodynamic testing, and then the last 20 years I spent in automotive testing around engine and powertrain testing.
Mike Golda:
So quite a diverse background, Bill.
Bill Collet:
Yes, I think so.
Mike Golda:
So what's exciting about this is your background, which I want to spend more time talking about today, which is the transmission application primarily revolving around the use of AC Dynamometers and their versatility as this application being used. So can you tell me a little bit about your experience that you've had with the transmission testing in regards to why do we test transmissions? Is it similar to engine? How are we testing?
Bill Collet:
Well, the main purpose we want to test the transmissions because ultimately the OEMs want to be delivering a product to their customers that is durable, has good shift quality, has a smooth ride. So all those things come into play with what the manufacturers are trying to accomplish when they do the testing. It's an advantage for them to do the testing in a test cell, as opposed to putting an engine and powertrain or the engine and transmission in a prototype vehicle, then having to put that vehicle on the road. You have the engineers out on the road, you've got a lot of times the conditions are not repeatable. So if you can put this in a test cell and you can run multiple scenarios over and over again and make some changes to the calibrations, you can see what those effects are with a very controlled environment.
Mike Golda:
So similar to engine testing, then you're trying to achieve the same thing without spending all the money and time actually in the vehicle. You're trying to bring it into a more controlled atmosphere inside the test cell. Is this all industries that the transmission applies to, all in any and all industries, or is it specific to automotive or all industries that utilize transmissions?
Bill Collet:
Well, my familiarity is with the automotive industry, but ultimately, across all industries where you have some kind of an engine or a vehicle with a transmission, you need to make sure that it's going to run properly and it's durable. Obviously, when you get into consumers and automotive or just personal passenger vehicles, they're going to be a little bit more picky when it comes to the performance of that transmission and the smoothness of their ride and quality of their ride.
Mike Golda:
Okay. So all the functionality of everything that the customer takes for granted, or they're driving in their vehicle and everything's just from a standpoint of driving in their vehicle, it's quiet, it's smooth running, it shifts. Well, this is all part that leads into all the work that's done in the background in the transmission testing arena and the calibration of the transmission. Right. Just as well as the calibration of an engine. There's calibration of the transmission, too.
Bill Collet:
Absolutely.
Mike Golda:
Okay, so when we look at the types of transmission testing are more so the levels. So we talk about the development work, the thing that the engineers work on to develop the next transmission or the next calibration in a transmission. So there's that aspect, but there's also once they do that, then they have to prove it out or basically run it for X amount of hours. The durability aspect of it, right?
Bill Collet:
That's correct.
Mike Golda:
Okay, so similar to the engine then.
Bill Collet:
Yeah, I've done a lot of durability work where you're setting up the transmission with a prime mover. A prime mover means basically it's what's driving the transmission as opposed to the engine. So you're just connecting the transmission directly to input dynamometer.
Mike Golda:
Okay.
Bill Collet:
And then on the back end of that, you could have anywhere from one dynamometers to four dynamometers. If you're talking about a rear wheel drive transmission, you might have one output dynamometer on the rear drive shaft, or you might have a differential in place, and then you have two dynamometers for each rear wheel. Or if you talk about a front wheel drive application, you've got two dynamometers on each of the front wheels off the half shafts. Or you could even have a full four output dynamometer configuration where you get all four wheels. Basically, where you have the two half shafts for the front wheels, a rear drive shaft through a PTU, and then a rear differential, and then two dynamometers on the rear wheels.
Mike Golda:
So literally, you could have a setup that is absent completely of the engine itself. So you have a transmission in the center, you have a motor that's driving it. And if it's a four wheel drive application, you're saying you'll have a dynamometer at each of the wheels as well.
Bill Collet:
That's correct, yes.
Mike Golda:
So that's pretty incredible. So that must give you extremely good tight control based upon an AC motor application. Yes?
Bill Collet:
Yes and then, of course, the next step is I've done a lot of times where we don't have a prime mover and we actually have an engine and transmission together, which I refer to as a powertrain. And then you don't have an input dynamometer, and then you have the engine and the transmission and the interfaces between those two and how they transfer torque and so forth, and how they're working together. And then there's a whole different aspect of how those two interact with each other when it comes to the engine calibration and transmission calibration.
Mike Golda:
So how do they a question delving more into the which is pretty neat, the application where you're minus parts of the vehicle and you're simulating it with the AC dynamometers. How do they replicate what is seen on the road to what's done inside the test cell? How do they replicate that?
Bill Collet
Well, when it comes to the wheels there's what we call a road load application. So in other words you're simulating the inertia of the vehicle and you're simulating traction control or wheel loss. So what we do is we have road load application or a road load application where basically it's like F equals MA. So force equals mass time acceleration. So you're taking into account the inertia of the vehicle and then it's sending a speed command to the wheels to simulate exactly as if you had that transmission in a full vehicle running on the road.
Mike Golda:
So is it the process they're physically instrumenting the vehicle that's actually on the road and they're pulling data from that and they're inputting it back into the test cell?
Bill Collet:
Again, not so much. I mean like a road load simulation is really that's just pure mathematics in terms of it's just a simplification of how much does the vehicle weigh. So if you've got so much force that you're applying to the system, what kind of acceleration are you going to get based on the mass of the vehicle. So that way you get more of kind of a realistic torque and speed input against a transmission as you would as if it was a vehicle on the road. But now there's other times I've been involved in where you take that to the Nth level and you actually use what we call like hardware in the loop where typically you think of hardware in the loop as software and instrumentation or I should say software and hardware of a vehicle. But in this case the hardware is going to be the engine and the transmission and you can use a vehicle model and that vehicle model. Then the input to that vehicle model would be the torque that the engine transmission outputs that goes into the vehicle model crunches through all the simulation of the vehicle. And what's going to come out is a speed output to the wheels. And when I'm talking about this we're doing this at many, many times a second. So when you get that kind of fidelity you can actually get repeatable and verifiable shift quality data the same as if you would if you actually had an engine and a transmission in a vehicle, a prototype on the road.
Mike Golda:
So in essence you've got the opportunity to change one variable at a time and consistency. See what the impact of the result exactly.
Bill Collet:
It's very repeatable. If you got a technician out on the road or on the track and they're doing some tip ins whatever with the throttle.
Mike Golda:
Meaning what do you mean by tip in.
Bill Collet:
Tip in means when you slam on the accelerator.
Mike Golda:
Okay. Foot to the floor.
Bill Collet:
Foot to the floor. Yeah. So that timing of that, there's going to be little variations and so forth. If you actually have a human in the vehicle doing that, or there's going to be variations in the wind and so forth. So if you can do that in a test cell, everything's repeatable, you can make a little tweak to the calibration and you know exactly that that change is due to your calibration change and not some other parameters that you some other aren't able to measure.
Mike Golda:
Yeah, this is pretty cool stuff. So the challenges what are some of the challenges that you face when you're trying to do transmission testing? I mean, you may have covered it already with the replication of the results that you really see in the real world, but what are some of the challenges that you've seen that have caused you to spend more time working through these potential issues?
Bill Collet:
Well, the big thing is you have to have people that know what they're doing in terms of controls. When you've got five dynamometers trying to work together, you want to make sure that they're all in sync and they're doing what they need to do. In other words, you don't want one dynamometer going clockwise, the other one going counterclockwise.
Mike Golda:
That would be detrimental to health.
Bill Collet:
So that's one thing. Another thing is when we talk about some of these shift quality and some other things like wheel slip, that kind of thing, you have to have a dynamometer with very low inertia, because we're talking about there's going to be instances when you have very high accelerations. And if you've got a dynamometer with a lot of inertia, it doesn't have the oomph to be able to force those fast accelerations. So the less inertia you have on the dynamometer, the easier it is to react and perform and have those high accelerations.
Mike Golda:
So is that one of the reasons permanent magnet motors are used?
Bill Collet:
Pretty much, yes.
Mike Golda:
Okay, all right. So are there other ways to test transmissions outside of the test cell or other ways to test transmission? The best way to test a transmission? What's your opinion?
Bill Collet:
Well, yeah, I mean, like I said, a lot of times, it's done with putting your prototype transmission and or engine in a prototype vehicle, putting it on the road, instrumenting that vehicle, collecting data real time as you're driving on the road or on the track, test track. I haven't been involved in that kind of testing in my career. All my career has basically been the work doing in a test cell itself with dynamometers. But that's what I'm familiar with.
Mike Golda:
Okay, well, Bill, looking into the future, do you see things changing in the future as far as how we test or the equipment we're using to test?
Bill Collet:
Yeah, I think you're going to see more and more like I talked about with the simulations. So there was always this vision. An OEM's vision is to be able to test everything without ever having to put together prototype. The less prototypes they put together, the cheaper it is, the faster their development time is and the quicker they can put a new vehicle or a new concept on the road and as cheaply as possible. So I think this day and age, with the computing power of the computers, they can be running these simulations real time and doing a lot of calculations very fast so you can get that fidelity that is needed to really basically correlate to what it would actually do in a vehicle in a row.
Mike Golda:
Yeah. My personal opinion is I don't know what yours is, Bill, but my personal opinion is the 35 years I've been doing these discussions are always been doing everything possible not to have to physically put something in a test. Cell and test it to run the models, to be able to test it on a PC or a computer without having to stick it in a test cell. But the reality is, no matter how efficient we are and no matter how much technology changes, again, it's my personal opinion is there will always be some form of testing inside of a test cell. I don't think it'll ever go away. I think we've made strides. I think technology has driven so we are more efficient outside the test cell and the models are becoming more robust in what we do. But I always think there'll be an aspect of it. You always have to get inside a test cell at some given point in time.
Bill Collet:
Yeah, I absolutely agree. When it comes down to even durability, you got to run it through its paces to make sure that engineers, they know their thing and they know their math and so forth. But eventually you've got to actually put it into test cell and verify that your assumptions are correct.
Mike Golda:
Yeah. Well, Bill, it's been a pleasure. I appreciate you coming on board and talking about application of transmission testing. And we hope to have you in another future episode because think this is unfinished business.
Bill Collet:
Oh, thank you very much.
Mike Golda:
All right.
Diane Nossal:
Thank you for listening to Dyno Insites presented by Froude. If there are any engine testing topics you would like us to discuss, we'd love to hear from you. Please email us at podcast@froudedyno.com.